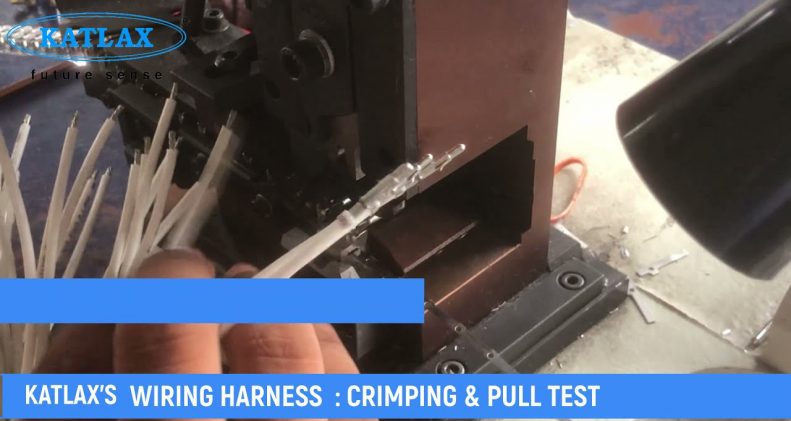
From automotive to medical devices, crimping is a common manufacturing process that spans various industries. Regardless of where it is used, it can suffer from the same quality issues.
A crimp is a process in which two pieces of metal (or some other malleable material) are joined by compressing them together through a process of deformation such as bending.
Crimping is often used for wire connections, where in-field performance of the final product will depend on electrical current passing through the crimped connection.
Common causes of crimp defects
- Missing wires or terminals
- Missing or soft crimps
- Missing strands or ears
- Debris caught in the terminal
- Double crimps
- Incorrect wire gage
- Improper placement
Standards and methods
A standard quality assurance test for crimp is the destructive pull-test. This is both time-consuming and costly. There are many standards to adhere to and each manufacturer or user might have different requirements to fulfill. But one thing in common is that international and industry standards all prescribe procedures for testing the tensile strength of wire terminals in a repeatable manner.
It is essential that there is no jerking or sudden application of force. This is the reason why standards state that there should be a ‘constant rate of pull’ and most define a pull rate at which tests should be performed.
Although standards define a minimum acceptance-value for the pull force according to the wire diameter and AWG conductor size, it is of greater importance to the manufacturer and user to know that joints can definitely sustain higher loads. So, an increasing axial force is applied to the connection until either the terminal and wire separate or the wire breaks.
Nice video